WHAT DOES TORQUE MEAN AND HOW DOES IT IMPACT YOUR TOOLS?
There’s a lot to consider when buying a new power tool. Will a cordless power tool perform as well as a corded one? Do I need 1 or 2 gears? And what on earth do people mean when they talk about the amount of torque or torque settings? To help demystify the tool jargon, we’re going to run you through the basics of what torque Settings are, why it matters and when you’ll need to use it to give you the power to make the right choice on your next tool purchase.
WHAT IS TORQUE FOR POWER TOOLS?
Torque, measured in Newton Metres (Nm), is the force that causes an object to rotate and is the best gauge to see how powerful your drill or impact driver is and the higher the number in newton metres the more twisting force it will deliver.
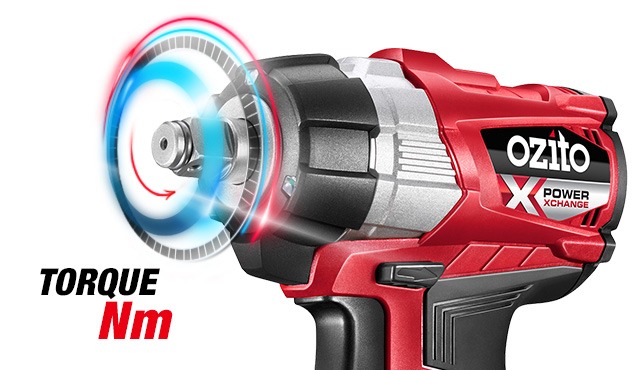
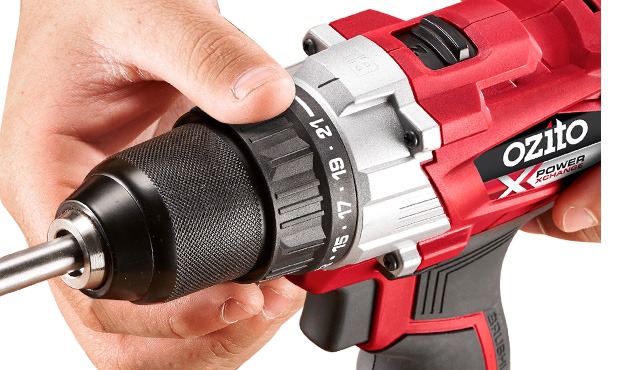
WHAT ARE TORQUE SETTINGS & HOW DO I USE THEM?
Think of torque settings like a clutch in a car. When you press the clutch pedal all the way in the wheels on the car lose power and speed. When you release the clutch pedal all the power goes to the wheels and they spin faster.
The trigger on a drill acts like the accelerator pedal in a car, the harder you press the trigger the faster the drill spins.
You might be wondering ‘Why would I ever want my power tool be less powerful?’
The truth is there are a number of occasions where you might want to turn down the torque to give yourself more control. Variable torque settings makes your drill more versatile and allows you to complete a wider variety of jobs with the same tool.
For example, if you are driving screws into a soft material like wood your best bet is to turn down the torque. If you leave your drill at top torque, you’re likely to run into a couple of problems.
Over driving your screws
Because you’re on the top setting you’ve got less control over how deep you’re driving your screw, so it’s easy to over shoot the mark which can split the wood and ruin your project.
Stripping the screw head
If you’re driving your screws into a hard wood it’s likely that you won’t feel the resistance when the screw has been completely driven. As the drill driver spins the screw has nowhere to go and as a result your screw head gets stripped making it impossible to remove the screw in the future without damaging your project.
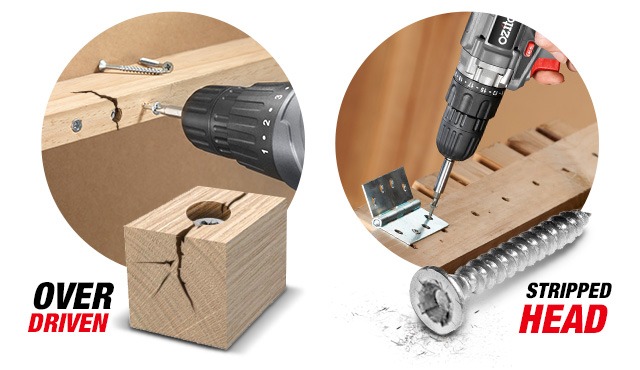
THE BASIC GUIDE FOR TORQUE SETTINGS.
When driving screws in the harder the material the lower speed and more torque you’re likely to need. Getting these settings right helps you to control the depth of your drilling without causing any damage.
When drilling holes the harder the material the higher the speed to get the best result.
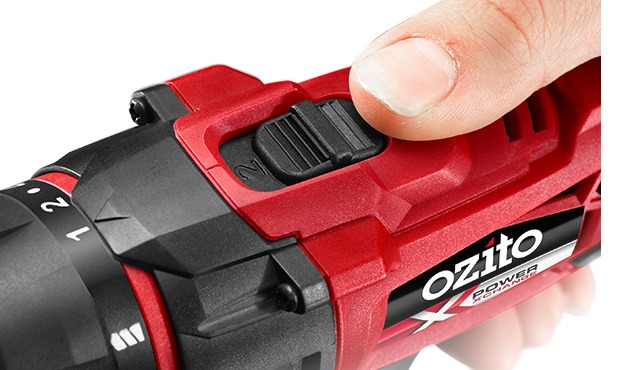
SO WHAT DO I LOOK FOR?
Torque Settings
The more settings the finer your control while working.
Newton Metres (Nm) on drills:
4 to 15Nm is fine for all of those smaller screw driver tasks around the home.
15 to 35Nm is a great all-rounder to drill and drive medium sizes screws and hole drilling.
35Nm upward will tackle all of those more serious project with bigger screws and holes
Gear box
A 2-speed gearbox will usually give you a higher RPM (Revs Per Minute) than a single speed and this gives even more control over your project.